Posted: Jan 22, 2015 |
Size matters: The importance of building small things
|
(Nanowerk News) Strong materials, such as concrete, are usually heavy, and lightweight materials, such as rubber (for latex gloves) and paper, are usually weak and susceptible to tearing and damage. Julia R. Greer, professor of materials science and mechanics in Caltech's Division of Engineering and Applied Science, is helping to break that linkage. In Caltech's Beckman Auditorium at 8 p.m. on Wednesday, January 21, Greer will explain how we can give ordinary materials superpowers. Admission is free.
|
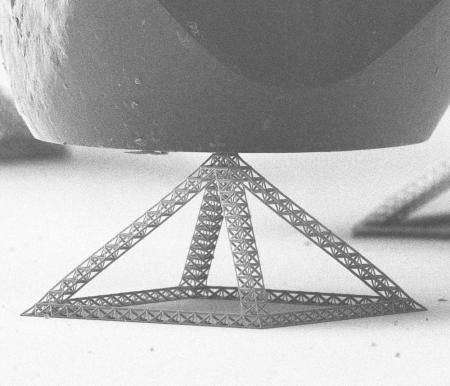 |
A fractal nanotruss made in Greer's lab. (Image: Lucas Meza, Greer lab/Caltech)
|
Q: What do you do?
|
A: I'm a materials scientist, and I work with materials whose dimensions are at the nanoscale. A nanometer is one-billionth of a meter, or about one-hundred-thousandth the diameter of a hair. At those dimensions, ordinary materials such as metals, ceramics, and glasses take on properties quite unlike their bulk-scale counterparts. Many materials become 10 or more times stronger. Some become damage-tolerant. Glass shatters very easily in our world, for example, but at the nanoscale, some glasses become deformable and less breakable. We're trying to harness these so-called size effects to create "meta-materials" that display these properties at scales we can see.
|
We can fabricate essentially any structure we like with the help of a special instrument that is like a tabletop microprinter, but uses laser pulses to "write" a three-dimensional structure into a tiny droplet of a polymer. The laser "sets" the polymer into our three-dimensional design, creating a minuscule plastic scaffold. We rinse away the unset polymer and put our scaffold in another machine that essentially wraps it in a very thin, nanometers-thick ribbon of the stuff we're actually interested in—a metal, a semiconductor, or a biocompatible material. Then we get rid of the plastic, leaving just the interwoven hollow tubular structure. The final structure is hollow, and it weighs nothing. It's 99.9 percent air.
|
We can even make structures nested within other structures. We recently started making hierarchical nanotrusses—trusses built from smaller trusses, like a fractal.
|
Q: How big can you make these things, and where might that lead us?
|
A: Right now, most of them are about 100 by 100 by 100 microns cubed. A micron is a millionth of a meter, so that is very small. And the unit cells, the individual building blocks, are very, very small—a few microns each. I recently asked my graduate students to create a demo big enough to be visible, so I could show it at seminars. They wrote me an object about 6 millimeters by 6 millimeters by about 100 microns tall. It took them about a week just to write the polymer, never mind the ribbon deposition and all the other steps.
|
The demo piece looks like a little white square from the top, until you hold it up to the light. Then a rainbow of colors play across its surface, and it looks like a fine opal. That's because the nanolattices and the opals are both photonic crystals, which means that their unit cells are the right size to interact with light. Synthetic three-dimensional photonic crystals are relatively hard to make, but they could be extremely useful as high-speed switches for fiber-optic networks.
|
Our goal is to figure out a way to mass produce nanostructures that are big enough to see. The possibilities are endless. You could make a soft contact lens that can't be torn, for example. Or a very lightweight, very safe biocompatible material that could go into someone's body as a scaffold on which to grow cells. Or you could use semiconductors to build 3-D logic circuits. We're working with Assistant Professor of Applied Physics and Materials Science Andrei Faraon [BS '04] to try to figure out how to simultaneously write a whole bunch of things that are all 1 centimeter by 1 centimeter.
|
Q: How did you get into this line of work? What got you started?
|
A: When I first got to Caltech, I was working on metallic nanopillars. That was my bread and butter. Nanopillars are about 50 nanometers to 1 micron in diameter, and about three times taller than their width. They were what we used to demonstrate, for example, that smaller becomes stronger—the pillars were stronger than the bulk metal by an order of magnitude, which is nothing to laugh at.
|
Nanopillars are awesome, but you can't build anything out of them. And so I always wondered if I could use something like them as nano-LEGOs and construct larger objects, like a nano-Eiffel Tower. The question I asked myself was if each individual component had that very, very high strength, would the whole structure be incredibly strong? That was always in the back of my mind. Then I met some people at DARPA (Defense Advanced at HRL (formerly Hughes Research Laboratories) who were interested in some similar questions, specifically about using architecture in material design. My HRL colleagues were making microscale structures called micro-trusses, so we started a very successful DARPA-funded collaboration to make even smaller trusses with unit cells in the micron range. These structures were still far too big for my purposes, but they brought this work closer to reality.
|
Named for the late Caltech professor Earnest C. Watson, who founded the series in 1922, the Watson Lectures present Caltech and JPL researchers describing their work to the public. Many past Watson Lectures are available online at Caltech's iTunes U site.
|